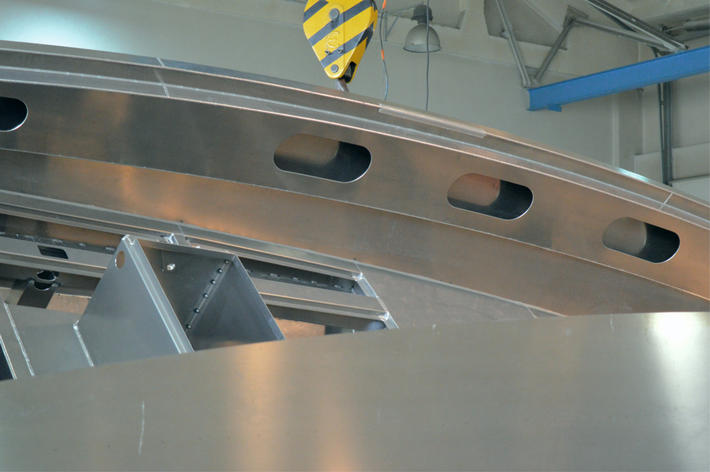
Aluminum alloys for the naval sector
The use of aluminum in boats has been a growing reality for many decades, and this is because the light metal is able to mediate the needs of the designer, the builder and the end user very well. Added to this is the intrinsic environmental sustainability of aluminum which makes it the material of first choice for the most innovative eco-sustainable projects of pleasure and commercial boats.
Aluminum is one of the four basic materials for shipbuilding, together with wood, steel and composite materials of the GRP (Glass ReinforcedPlastics) family. Wood was the protagonist material in this type of application until the end of the 19th century, today it is chosen almost exclusively for special vessels, such as high-end yachts. Steel replaced wood by virtue of more attractive characteristics, from mechanical resistance, to cost, to availability, to simple workability, having limitations such as high volume density and modest resistance to corrosion.
Aluminum appeared as a candidate for use in shipbuilding in the last years of the 19th century, when its penetration into many application segments was still just beginning. It clearly came to the attention of operators as a very interesting material for shipbuilding due to its lightness, advantageous strength/weight ratio and excellent resistance to corrosion. Composites and reinforced fibers are the most recent materials for use in shipbuilding. Compared to traditional wood, they offer significant advantages, from low maintenance to good resistance to corrosion.
It is clear that the factors that make one or another of the different materials preferable are numerous, from the size of the boats to the expected performance, to the numerical consistency of the series to be produced.
Aluminum, with the different types of commercial alloys, expresses an interesting balance of:
- Mechanical and impact resistance;
- Lightness;
- Durability;
- Aesthetic and functional properties;
- Safety and reliability;
- Simplicity of processing and maintenance.
The use of aluminum in the nautical and naval sector
Historically, we remember experiences with aluminum at the beginning of the last century, when very little was known about this material. Even then, however, the new, somewhat mysterious metal aroused curiosity and interest because it was light, beautiful to look at, resistant and resistant to corrosion, therefore suitable for new solutions for a vehicle that moves in water.
We are obviously talking about absolutely cutting-edge applications, while for real market penetration we had to wait until the years around 1940, with the use in military ships of laminates of Al-Mg plastic transformation alloys, known in shipyards under the commercial name Peraluman.
Today aluminum alloys are still young, but there is no longer anything mysterious about them: the performance, technologies and processing and finishing methods have been known for years, as well as the most suitable design criteria for use in pleasure boats, commercial and military use.
The alloys historically of greatest interest for uses in the naval sector are the compositions of the 5000 Al-Mg series: they present excellent weldability and have a high resistance to corrosion (especially in a marine environment). These alloys find their characteristic use as laminates. We remind you that other typical applications of 5000 alloys include, in addition to boats, road signs, cryogenic tanks, decorative and architectural finishes, cans and household appliances.
Aluminum for naval applications
The subsequent developments in the use of aluminum in the naval sector were the superstructures of merchant ships, pleasure boats and a widespread diffusion in equipment and accessories, especially as extruded semi-finished products.
We are talking about the 6000 Al-Mg-Si extrusion alloys, with good hot formability, a good combination of properties and treatable with a simple and economical tempering cycle. These alloys have a composition based on different combinations of the main alloying elements magnesium and silicon, and on the addition of smaller quantities of Cu, Mn and Cr. Overall, they have good mechanical characteristics, high surface finishing qualities, high resistance to corrosion, easy weldability.
Aluminum extrusions have many applications because when the designer needs a component with an intricate shape, characterized by a constant section and a certain length (particularly creative from both a functional and aesthetic point of view), this semi-finished product solves many problems.
With extrusion technology, it is in fact possible to reproduce complex geometries, which traditional carpentry would allow to obtain only at very high costs and with poor reliability of results: an example are the sections used for the creation of the fencing, often also designed to accommodate rubber parts, where the ship-dock contact is continuous and not just occasional. In terms of complexity, closed extrusions are the most striking example, even if modern joining technologies (especially laser welding) today allow to produce similar sandwich panels without resorting to extrusion and also allow to think of the same not necessarily in light alloy, but also in high-strength steels of modest thickness, which have become competitive on a technical-economic level for specific applications, such as garage decks, flight decks and ramps.
Foundry alloys and castings for naval applications
Finally, we have foundry alloys for castings, with many technologies available to meet the requirements imposed on the component. Each process offers very specific advantages and benefits, especially if used taking into account the characteristics of the alloy to be cast and the type of component to be produced.
From a metallurgical point of view, similar considerations apply to foundry alloys as to workable alloys. There are different families of alloys (those for use in the marine sector are essentially non-heat-treatable Al-Si and Al-Mg systems, and heat-treated Al-Si-Mg) with different foundry properties (castability, susceptibility to shrinkage, brittleness), different mechanical characteristics and different technological properties (machinability, resistance in aggressive environments, possibility of surface finishing, weldability).
In conclusion, aluminum alloys have been finding increasing applications in the shipbuilding sector for years. The light metal is still young but the performance characteristics, technologies, processing and finishing methods and design criteria are well known.
Furthermore, aluminum is the material for energy saving, environmental protection, economic competitiveness, satisfaction and safety of end users. It is increasingly establishing itself in the field of transportation and for this reason it has expressed excellent developments in the naval sector.
With the heritage of decades of knowledge of the aeronautical industry and with the urgency of the automotive industry to manufacture lighter, less polluting and socially sustainable vehicles, a new technological culture has been created in a few years for a wide diffusion of aluminum in transportation. From this process, the boat sector has also drawn a new stimulus for innovation.
Source: A&L Aluminium Alloys Pressure Diecasting Foundry Tecniques