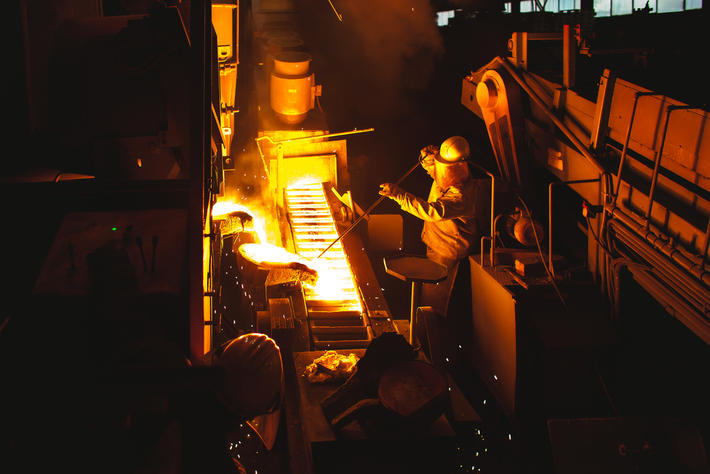
Aluminum Foundries and Insulating Sleeves: Developments in Exothermic Feeding in Aluminum Castings
In aluminum foundries, the use of insulating sleeves in a wide variety of materials has been common practice for many years. A new exothermic sleeve material for non-ferrous alloys and casting applications has recently been introduced for the first time.
The new recipe called FEEDEX NF1 has been developed specifically for the aluminum industry and adapted to existing requirements. The exothermic reaction starts quickly and the reaction takes place slowly and steadily, resulting in a significant improvement in feeding. This results in low emissions. FEEDEX NF1 feeders are available in many different versions and eliminate the need for adding exothermic powders.
Isothermal feeders for aluminum applications
The use of insulating feeders is a common practice in aluminum foundries. In this sector, there are several products on the market with different shapes. In most cases, the materials are made of fibers or spherical materials. In both cases, organic or inorganic binders are used.
If the insulating property is not sufficient or if the size of the sleeve is limited, very often exothermic powders are also applied and added. These powders (such as FEEDOL) start an exothermic reaction when they come into contact with liquid aluminum and provide their energy by activating on the surface of the sprue to slow down solidification, adding extra energy to the liquid metal reservoir in the sleeve to extend the feeding capacity. This technique is also a common practice.
However, this exothermic powder application process has a number of disadvantages:
- The powder application must be done manually, so the supply is often inconsistent; the operator may have difficulty applying the powder to all feeders at the same time and in a repeatable manner;
- In the case of very large castings, adding exothermic powder to all sleeves is very time-consuming;
- The sleeve must be accessible for addition, so emissions from the FEEDOL powder are released into the foundry environment.
With these new products, exothermic feeders for aluminium applications are available for the first time. These products are made with a new exothermic recipe developed to make the application of exothermic powders unnecessary. Upon contact with liquid aluminium, ignition begins within the first 30 seconds. Until now, this type of technology has only been used for ferrous applications and therefore not suitable for aluminium foundries. This exothermic reaction proceeds slowly, steadily and provides significantly delayed solidification of the metal in the sleeve and thus long-lasting feeding performance.
The modulus extension factor of 1.3 to 1.5 for insulating sleeves becomes 1.55 to 1.65 for FEEDEX NF1. These values lead to a number of advantages:
- Manual application of exothermic powder becomes superfluous;
- Feeders can be completely formed and covered (closed sleeves) leading to a reduction in emissions.
Even with open FEEDEX NF1 sleeves, reduced emissions can be detected. Exothermic sleeves having a better efficiency can lead to a reduction in sleeve size and consequently to a reduction in remelting costs.
Insulating sleeves for aluminum foundries
Feedex NF1 sleeves can be used without any problems in both automatic plants and core molding, as they have a higher mechanical resistance.
In contrast, feeders with a lower force can break or deform during the molding process.
The exothermic reaction of this type of sleeve starts only a few seconds after filling, continues slowly and uniformly. This makes the addition of exothermic powders obsolete.
The fast, constant and long-lasting reaction make these insulating sleeves an excellent alternative to conventional insulating feeders. The high resistance of the material makes them suitable for use on automated molding lines. The improved feeding effect can lead to a reduction of the feeder size and therefore to a saving of recycled material. The manual addition of exothermic powders is no longer necessary, which increases the stability of the process.
Source: In Fonderia – The magazine of the Italian foundry industry