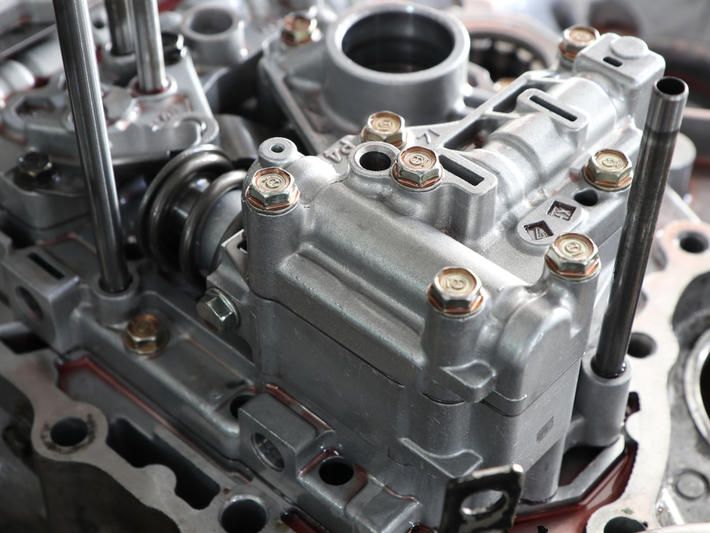
Experimental and numerical analysis of casting and filling defects in AlSi7Cu0.5Mg alloy castings
Light alloy foundries currently need to produce high quality components, with complex geometries and short development times, while maintaining a high yield of the production process and limiting waste. Minimizing the production of non-conforming components has a double advantage:
- An increase in productivity, therefore in the company margin;
- A reduction in costs related to energy expenditure in the melting phase.
The numerical simulation software of foundry processes are therefore an essential tool to allow companies to remain competitive on the market. The accurate prediction of the formation of defects in the castings of light alloys in the filling and solidification phase allows the implementation of improvements aimed at increasing the integrity of the final component.
Among the casting defects that most compromise the performance of a casting are oxide bifilms. These defects, generated during the metal preparation, pouring and filling phases, act as promoters for the formation of shrinkage porosity, gaseous porosity and hot tearing. A component without bifilms would be intact, also devoid of any defect generated during the solidification of the material.
The development of numerical simulation software capable of accurately predicting the formation of defects in the castings of light alloys filling would facilitate the implementation of process and product design improvements, aimed at reducing waste and increasing the company margin.
This study aims to evaluate the reliability of numerical models for predicting the formation of casting and filling defects implemented in FLOW-3D Cast, a commercial software for the numerical simulation of foundry processes. This evaluation is performed by comparison with experimental data.
A preliminary numerical analysis made it possible to identify the process parameters that favor the formation of casting and filling defects. For the casting process, an AlSi7Cu0.5Mg (EN AC-45500) alloy and two mold geometries were chosen:
- the mold for the production of separately cast specimens with circular section;
- the mold for the production of separate cast specimens with rectangular section.
The analysis of the numerical outputs of the fraction of the volume of trapped air and the concentration of defects generated on the surface in contact with the atmosphere made it possible to identify the most critical casting conditions, then reproduced experimentally.
To promote the final amount of casting defects, all castings were cast without the filter. The repeatability of the experimental tests was verified by monitoring the variation in temperatures during the casting process and filming the mold filling phase. In addition, the data collected during the experimental campaign allowed the numerical implementation of the process through Reverse Engineering operations.
The castings were subsequently characterized from the microstructural point of view. After analyzing the chemical composition of the alloy, the spacing between the secondary interdendritic branches (SDAS) was measured and the distribution of defects generated by the presence of oxide bifilms was mapped.
From the analysis of the results obtained, it is clear that the software accurately models the fluid dynamic behavior of the metal; in fact, there is a correspondence between the simulation of the mold filling and the videos recorded during the experimental campaign. The consistency between the simulated solidification times and the experimental times was also verified.
The accuracy with which the software predicts the entrapment of oxide bifilms was evaluated by comparing the experimental defect mapping and the numerical outputs of the trapped air and the generation of defects in the jets of light alloys. In the mold for rectangular section specimens there is a good correspondence between numerical and experimental data: high density of defects can be identified in the upper central part of the filter and in the useful section.
On the opposite, in the circular section casting divergences between numerical and experimental results can be identified. In the simulation, the areas adjacent to the surfaces in contact with the atmosphere show a much higher concentration of jet defects in light alloys than that detected experimentally. Furthermore, the defects are mainly concentrated in the area downstream of the filter, an area which in reality is almost intact. These divergences are related to the overly simplifying model used to predict the formation of casting and filling defects.
It can therefore be used that the reliability of the software in modeling the fluid-dynamic behavior of the metal and in predicting the formation of jets defects of the alloys in the internal zones can be verified. Some improvements to the computational code are instead necessary to predict the distribution of casting defects in areas adjacent to surfaces in contact with the atmosphere.
Source: In Fonderia - The magazine of the Italian casting industry, n. 2 – 2021