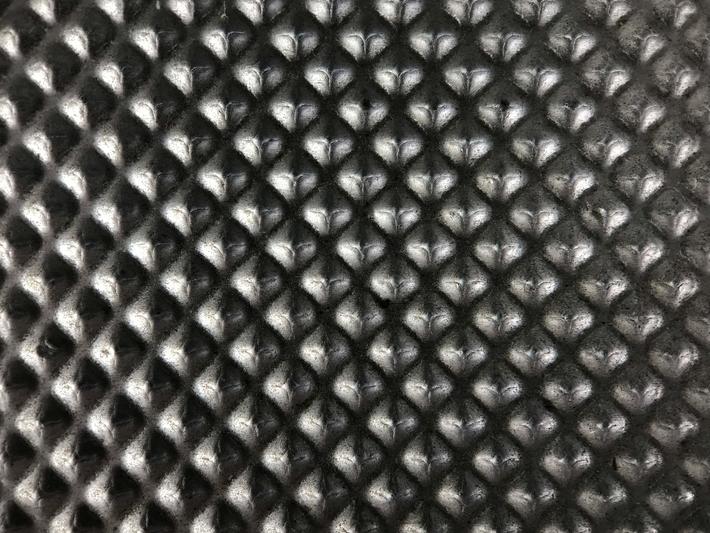
How many and what characteristics have foundries with aluminum castings
In Europe, there are two leading countries in the production of aluminum alloy castings: Germany and Italy. The majority of foundries (around 53%) are small and medium-sized enterprises, while large industries correspond to 47%. Specifically, most foundries (69%) produce diecastings, while 31% produce by gravity casting and low pressure.
The most common alloy is EN AB 46000 (Al-Si9-Cu3 (Fe)) used by 58% of foundries, followed by EN AB 43400 (Al-Mg-Si10 (Fe)) used in 38% of foundries. Four of the five most used alloys (EN AB 46000, EN AB 43400, EN AB 47100, EN AB 46100) are typical diecasting alloys.
The advantages of foundries with aluminum castings
To produce objects in aluminum alloys, die casting is the most economical and performing technology. Cast foundries are therefore an ideal interlocutor: they guarantee the customer the required piece, complete with finishes. The advantage is that, compared to bar machining , you save over 50% on the cost of the raw material and the cost of the molds is depreciable, being reusable for a complete series.
More specifically, aluminum casting foundries are competitive for the following reasons:
- Complex shapes with very small tolerances and high repeatability
- Thin thicknesses, in some cases even less than 1.5 mm
- High mechanical resistance
- High workability
- Low cost of raw material
- The die-cast components are more durable than plastic compared to any type of deterioration or deformation.
- Components with a high degree of aesthetic finish, therefore suitable for the furniture and lighting industry.
- Possibility to obtain from a mold various versions of an article by replacing pins or plugs.
- Inserts in different materials such as screws or bushings can be co-molded in the casting becoming in all respects an integral part of the same.
- Possibility to choose from a vast catalog of alloys with different mechanical characteristics.