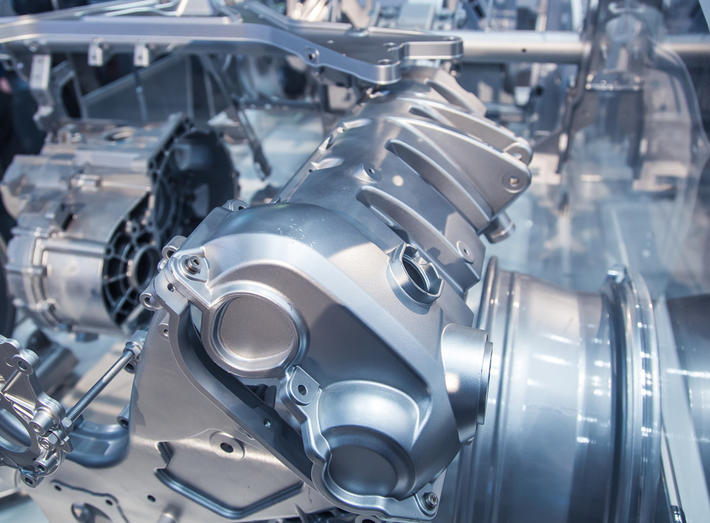
Why partnerships and innovation are the best strategies for aluminum: how to improve the production efficiency of the die casting industry
Companies that are flexible and open to change are more successful, and in the aluminum industry this means improving workflow processes to increase efficiency and sustainability.
One of the most important parts of running a thriving business is adaptability. Aluminum is a sustainable solution for many industries for this reason it is essential to create constantly evolving and innovative solutions in aluminum production.
Major manufacturers of aluminum laminates have been at the forefront of these efforts. Thanks to heavily funded project schedules, large investments have been made in continuous casting technologies. Despite the Covid-19 pandemic, many companies have completed the expansion of their aluminum plants, paving the way to further serve their key customers.
While the pandemic was certainly not on the agenda during these expansion plans, companies have been able to adapt. From start to finish, they implemented various health and safety measures to keep projects moving and, most importantly, to ensure that everyone, from employees to partners, stayed safe. As a result, several aluminum industries today are on track to achieve important goals for manufacturing their products using up to 100% aluminum scrap.
State-of-the-art Italian technology to improve the efficiency of the aluminum industry
Among the highlights of the designers are new tandem hot rolling mills produced by Italian companies, which work in unison with a casting machine and which are an integral part of expansion projects. The integration of continuous casting with the tandem rolling mill significantly increases productivity by allowing a plant to continuously laminate, divide and wind aluminum strips of large dimensions.
Among the technological solutions, it is worth mentioning the innovative cooling system that manages and regenerates the refrigerant with significant environmental benefits. In terms of automation, the process control system includes a model-based system developed to optimize the quality of the laminate.
Secondary aluminum and flat laminates for maximum efficiency in the die casting industry
The downstream transformation processes involving aluminum have an embedded sustainability factor, representing the circular economy at its best. Aluminum is 100% recyclable and, unlike most other metals, it does not lose its properties during the recycling process. Furthermore, recycling aluminum saves more than 90% of the energy needed to produce new metal.
For example, recycling an aluminum can instead of throwing it away saves enough energy to run a laptop for 11 hours. Also, recycling the same can could keep a 100-watt light bulb on for five hours. Overall, recycling one kilo of aluminum equates to energy savings of seven kilowatt hours of electricity. And rolled aluminum, as a whole, account for 40% of all shipments of aluminum products in the Western world, demonstrating its importance as a material for industry.
It is increasingly evident that in terms of innovation and global partnerships, the aluminum industry and its equipment suppliers are equal to the situation. As long as ingenuity and new ideas remain a priority for both aluminum producers and equipment manufacturers, the benefits of aluminum application will become even more evident in the decades to come.
Source: A&L Aluminum Alloys Pressure Diecasting Foundry Tecniques