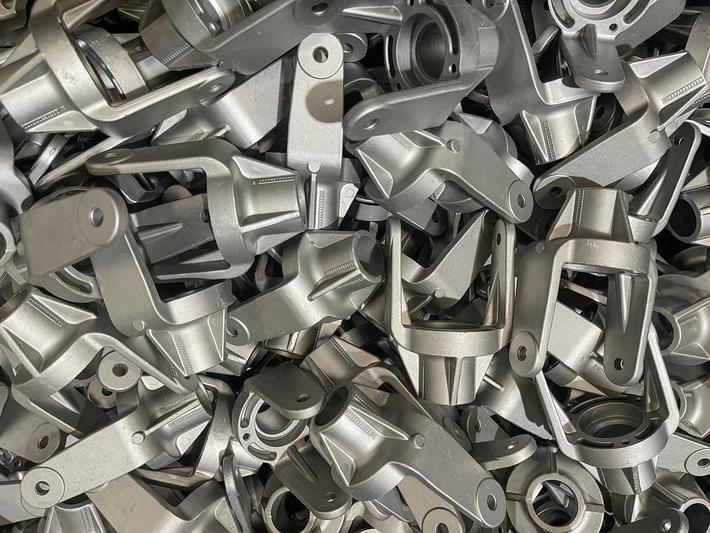
The importance of aluminum recycling: the key role of eco-sustainable aluminum
Aluminum lends itself very well to recycling, it has been a popular material for decades due to its characteristic of being a real energy bank: it requires a lot of energy to be produced in smelters starting from bauxite, but it conserves and returns just as much because it is recovered and can be melted and reused indefinitely, without loss of quality.
Aluminum scrap and its alloys can be reused with very low losses and without significant degradation of metallurgical and technological quality levels. Today, about 75% of all primary aluminum produced in just under 150 years is still in circulation and scrap collection rates vary from 10% to 90% depending on the regions and products.
High-value end-use sectors, such as automotive and construction, and middle-income countries lead collection rates due to the attractiveness of employment in the post-consumer scrap collection sector. Therefore, integrating secondary and primary aluminium is a cost-effective solution that materializes the extraordinary eco-sustainability of the light metal for:
- Save energy;
- Reduce sector emissions;
- Safeguard the environment.
On average, producing a ton of secondary aluminum generates only about 3% of the emissions associated with a ton of primary aluminum, with an energy consumption of 5% of that for primary production.
The great value of aluminum scrap refers both to pre-consumer scrap, deriving from production waste, transformations and processes of various kinds before the creation of the particular or final product, and to post-consumer scrap, such as sheet metal, car parts, old window frames, electrical cables, cookware, beverage containers, parts or components containing aluminum that have reached the end of their life. It is not waste to be thrown away, but rather a large reserve of light metal that can be put back into the cycle and reused.
Aluminum Scrap Recycling
The global aluminum industry has long been heavily engaged in collaborating with waste management sectors and governments to implement the necessary levers for scrap collection. This has not been purely theoretical, there are many practical cases that demonstrate the results actually achieved, there are already regional case studies on how to maximize collection rates, one can reason about the reasons why the average collection rates of packaging in Europe are for example different from Brazil. The case of old aluminum scrap from packaging is also a very interesting case study, it is certain that maximizing recovery and recycling in this area will depend on intelligent regulatory interventions, framed in a combination of new technologies and a careful organizational redefinition of collaboration along the entire value chain, from deposit return systems to the sorting phases and efficient collection infrastructure before the aluminum reaches the landfill. What must be kept in mind is that recycling old scrap aluminum properly is an operation that requires appropriate technological knowledge and skills, which include specific operations and treatments to achieve the regulatory chemical composition requirements.
The first problem is that of the chemical composition, we are talking about aluminum but we should instead be talking about dozens and dozens of different aluminum-based alloys, containing different percentages by weight of alloying elements such as copper, magnesium, silicon, zinc. Each alloy, depending on the type and content of the alloying elements, has its own characteristics of resistance, workability, weldability, wear resistance, conductivity, therefore different areas of preferential use, from car bodies to pots, cans, windows and electrical conductors.
There are many different alloys on the market, and the user companies generally require specific types depending on the use. It is clear that the old scrap from collection does not initially have a precise identity card regarding the chemical composition; so when in the post-war period the problem arose of inventing new solutions to the need for energy and financial resources, the concept of recovery and recycling took shape starting from the abundance of war scrap. Made up of a wide variety of alloys, these were dumped in bulk and sent to secondary foundries. It was still recycling, but destined for a market with lower demands and quality and continually decreasing in the recovery and reuse cycle of the scrap, after a certain number of cycles the material practically became waste.
Increasing secondary aluminium production
Today, the need to obtain, through recovery, quality alloys goes hand in hand with progress in the accurate identification of the chemical and metallurgical parameters of old scrap, so as to allow the best selection of the same according to the needs of remelting foundries. Maximizing the production of secondary aluminium, as has been clearly indicated in a recent study by the International Aluminium Institute (the non-governmental organization based in London, founded in 1972 to represent the global primary aluminium industry), will require an increase in the volumes of pre- and post-consumer scrap available for recycling, with the ambitious goal of reaching a percentage ratio of approximately 55/45 of global secondary/primary aluminium consumption by 2050.
This can only be achieved if industry leaders, policy makers and waste management operators are able to take concrete collective action on product design, collection and end-of-life dismantling. Scaling up secondary production is likely to face some obstacles. First, around 25%–30% of aluminium is lost in each use cycle due to post-consumer scrap collection loss and pre-consumer scrap processing loss.
Furthermore, secondary aluminium producers tend in many cases to avoid combining alloy-specific scrap batches, which still results in scrap downcycling that is an obstacle to creating efficient closed-loop systems.
Finally, we must not overlook possible problems caused by trading dynamics, which are not always predictable and controllable, such as, for example, possible regional bans on exporting scrap that could lead to situations of material shortages on the global market, with local consequences for the production of secondary metal. In our country, there has been no shortage of clear and precise positions taken in recent years on the possible risks for the local aluminum system, considering the clear downward trend in primary production in the EU and the haemorrhages of scrap towards many non-European countries. In this regard, we report several public complaints, such as the one in 2014 at the AFFG Round Table in Rome on the topic "The Italian aluminum industry: conditions for competitiveness", which briefly indicated the lines for the future development of the aluminum system.
Also worth noting is the critical position of Face, the European Federation of Aluminium Consumers, which in 2019, reiterating the positions expressed since 1998, once again denounced to the European Commission the burden on consumers due to the effect of the duty on raw metal, as assessed in the studies of the LUISS University of Rome on the EU downstream of aluminium. Pointing out in particular that: "... the 6% duty on primary aluminium costs EU transformers and users between 1 and 2 billion euros per year, the figure depends on the LME prices of the metal. Part of this greater burden is poured into the pockets of European raw producers, part benefits non-EU countries that export metal, especially those that enjoy tariff preferences with the Union. 55% of the primary imported into the EU comes from three countries (Norway, Iceland and Mozambique) that enjoy duty-free status". It is clear that there have been precise signals from the industry regarding basic needs for some time and with continuity. Decision makers at various national and European levels have had the right information, so the conditions exist to be able to define the correct industrial strategies and policies, but let's not forget the many obstacles that the numerous opposing lobbies continue to place, preventing an equal level of access for raw metal and hindering the path of secondary aluminum to fully assume the role it deserves in the decarbonization of the sector.
Source: A&L Aluminium Alloys Pressure Diecasting Foundry Tecniques