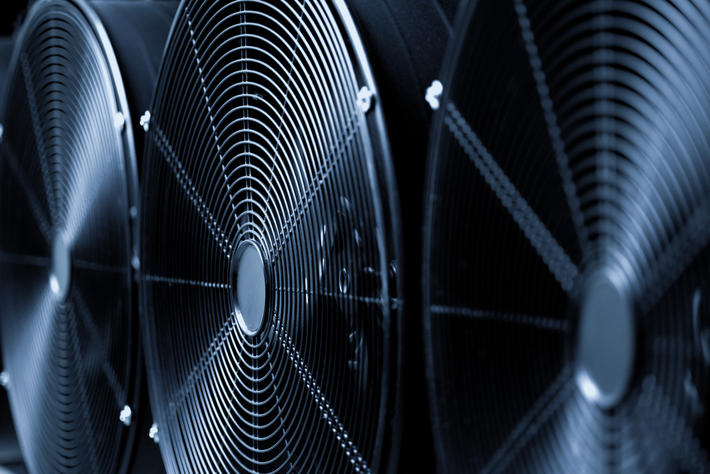
Energy savings in foundries: electrical consumption of fans
Industrial fans are widely used within foundries. Often with medium-large installed powers, these machines find themselves working in conditions that compromise their efficiency.
For over a year, energy costs have skyrocketed, making production unsustainable for manufacturing companies and in particular for foundries.
However, this crisis hides a significant opportunity: any investment that produces energy efficiency pays off much more quickly.
However, rapid actions are needed to reduce energy consumption - and therefore costs.
For several months we have been carrying out awareness and dissemination activities on the possible savings that can be achieved in a short time, with reduced budgets, on the consumption of industrial fans.
Why worry about the electrical consumption of fans?
These machines generally have a weight of around 14% of the total electricity costs. Not a huge share, but not an insignificant one either. Especially if we consider that very often fans - due to how they are purchased or how they are managed - lead to energy waste that can even exceed 50% of the energy used.
Furthermore, to cut the energy costs of fans, large investments are not necessary and in almost all cases the machine does not even have to be replaced.
However, an accurate analysis of the conditions in which the fans and the systems to which they are connected must work is essential.
No fan energy efficiency action will be truly effective if it is not based on a complete photograph of the actual functioning of the system in which it is installed and of the different production needs.
It is precisely in this preliminary analysis that the main areas of efficiency and energy saving can be identified.
How to find the typical conditions of energy waste in industrial fans installed in plants
Typical situations that cause inefficient operation of the fans have been identified.
The first of all is linked to the regulation of the flow rate delivered by the fan. In many applications, in fact, the system needs an air or gas flow rate that varies over time. The most emblematic case is that of the fans connected to the burners, which must supply a certain mass of air depending on the mass of gas to be burned. Unfortunately, it is common practice to carry out this regulation in an incorrect way not only from an energy point of view, but often also on the reliability of the fan itself.
The flow rate delivered is in fact managed by throttling a valve downstream of the fan. For adjustments within a small flow range, this method does not create mechanical problems. However, when adjustments are necessary that reach ratios of 1:10 with respect to the nominal flow rate, the fan is subjected to unstable operation with strong pulsations of the outlet pressure (and therefore flames in the burners), a dull and cyclical noise and failures of the bearings and/or the structure of the machine itself.
Regulation with a valve on the delivery in any case involves much higher electrical consumption compared to other regulation systems.
Another situation in which energy savings can be achieved in significant foundries is that of fans connected to extraction and dust collection systems. Since these systems are not "productive" but often imposed by law, the tendency is to purchase them at the lowest price. Obviously, therefore, the quality and efficiency of the fans installed will be adequate for the low purchase cost.
Ideally, when purchasing the system, it would be necessary to establish that the industrial fan has high efficiency, considering that it will work mainly with dust-free fumes. Unfortunately, it is very common to come across machines that have medium-low efficiency, between 50% and 60%. %.
According to analyses, however, it is possible to achieve consumption savings of at least 20% without having to replace the fan.
In addition to these two typical situations, there may also be others that can only be assessed from time to time with appropriate measurements. It must be said that in a foundry it is almost a given to find fans used for burners and others installed on dust collection systems. It therefore almost always makes sense to proceed with the next phase of measuring consumption and consequent analysis of efficiency scenarios.
From this second phase, once the operating parameters, the absorbed power and the various needs of the system in terms of productivity and flexibility have been acquired, it is possible to evaluate which energy efficiency strategy makes sense to adopt.
What energy efficiency strategies can be used for fans?
There are basically three different solutions to reduce the electrical consumption of fans in foundries:
1. Use a regulation damper (dapò);
2. Use a frequency changer (inverter);
3. Install a higher efficiency impeller.
The first two can be used to regulate the flow rate of the fan in place of the butterfly valves usually positioned on the delivery outlet. The regulation damper, called Dapò or IGV in jargon, allows a wider range of flow regulation. It is in fact possible to operate, without any problem for the fan or the system, with flow rates ranging from 10% to 100%.
The inverter, on the other hand, allows you to reduce the rotation speed of the fan, consequently decreasing the flow rate delivered. This efficiency strategy allows for greater energy savings compared to the dapò shutter. On the other hand, however, it cannot be used in cases where the flow rate must be reduced while maintaining a fairly similar value of pressure required by the system (for example with regenerative burners). In these situations, the phenomenon of pumping occurs with instability of the flames and damage to the fan itself.
The third strategy, however, is optimal in the case of aspirators installed on dust collection systems, which, as mentioned, are usually chosen more on the basis of price than efficiency. Without replacing the entire fan, it is possible to install an impeller which - for the same aspirated flow rate - is able to drastically reduce the power absorbed.
Finally, it is possible to use a mix of the three strategies seen, if this allows for a more effective reduction in consumption.
From theory to practice: case study of energy efficiency and reduction of energy consumption on combustion air fans
To better understand the correct method to use to reduce the electrical consumption of fans in foundries, we report below the case of an applied consultancy.
Four fans serving the same number of burners were analysed. The installed powers were as follows:
- Fan 1: 22 kW
- Fan 2: 22 kW
- Fan 3: 11 kW
- Fan 4: 30 kW
The air flow was regulated on each fan by means of a butterfly valve located in the downstream pipe. The fans had to operate in essentially two modes. Most of the time, the throttle was partially closed. In emergency cases, however, it was opened completely to allow maximum air flow.
Any energy efficiency action had therefore to take these two different needs into account. Reducing the size of the fans to avoid partializing the damper was therefore an unviable option.
Here is an example of how these considerations, which can only arise during a preliminary analysis of the system and fans, are fundamental to guarantee the success of the energy efficiency action.
Without evaluating all the real needs of the system, it would have been natural to decide to purchase smaller fans - and therefore with lower consumption - so as to avoid throttling the flow rates with butterfly dampers, effectively losing the possibility of managing the emergency situation.
After having understood all the real needs of the system, the next step is to measure the flow rate and actual absorbed power values. Once this data has been acquired, it is possible to start carrying out simulations considering the different strategies shown previously.
At this stage it is important to know industrial fans and how they work very well. The risk is in fact that of bringing the machines to work in unsafe and unstable conditions.
The case in question lent itself to using two of the strategies seen: replacement of the impellers with others with higher efficiency and regulation by means of a frequency variator (inverter). However, in agreement with the customer, only the installation of the inverters was opted for, as the benefit additional in terms of energy savings due to the new impellers was minimal compared to the increase in costs necessary for the intervention.
The power absorbed with an inverter takes into account the energy losses due to the introduction of the inverter and the lower efficiency with which the electric motor works when it operates at lower load conditions compared to the nominal power.
According to what the customer stated, the system operates 7,200 hours per year under normal conditions. Therefore, by multiplying the power saved by the number of hours per year, you can have a much clearer idea of the actual savings achieved, i.e. 183,600 kWh/year.
At this point we can anticipate a thought that might emerge in the reader's mind: "In any situation, can such huge savings be achieved, equal to almost 40% of initial consumption?".
The answer is negative. Such large reductions in fan energy costs are not always achieved. Sometimes even greater savings can be achieved, and in other cases an energy efficiency action is not economically convenient.
The preliminary analysis carried out for those asking to reduce consumption has the aim of evaluating whether or not the conditions exist to obtain an economic benefit worth the investment. It is not possible to guarantee energy savings from fans in foundries without first having carried out the preliminary analysis and field measurement campaign.
Source: In Fonderia – ll magazine dell’industria fusoria italiana