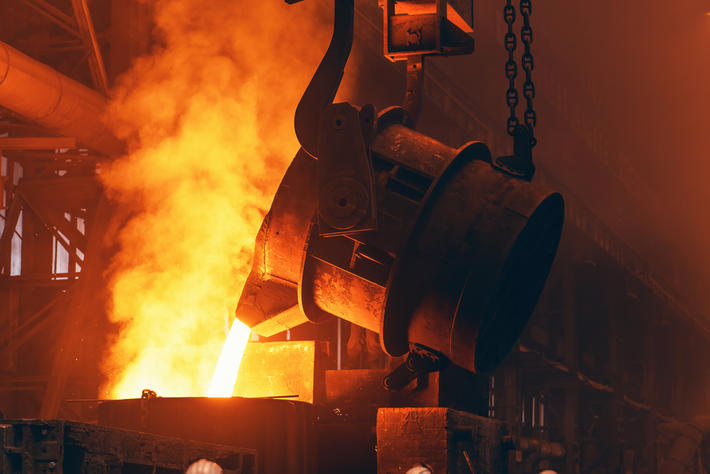
Powdered Sand Additives: Lithium-Free Additive Alternatives for Cast Iron, Steel and Aluminum Foundries
Productivity and efficiency are characteristics whose demand is always constant and constantly increasing in the foundry sector. At the same time, social and political changes are taking place. Awareness and sensitivity towards ecological problems and constant commitment to protecting the environment and conserving resources are topics on the agenda.
The objective of society and politics is to abandon the classic and proven combustion engines to move towards the electrification of powertrains in the short term. As part of this change, one raw material is gaining enormous importance: lithium.
Lithium is a key component for rechargeable batteries, but it is also an essential component of sand additives. The supply situation and above all the price trend are difficult to predict. Furthermore, the extraction conditions and efforts required for processing in South America have disastrous consequences for both the environment and local populations.
In this context, the aim is to develop new lithium-free sand additives capable of meeting the demands of foundries aimed at achieving sustainable and cost-effective production. By working closely with numerous foundries, notable successes have been achieved over the last 4 years. With these newly developed sand additives, foundries will be able to continue to meet both current and future requirements.
The growing importance of electromobility is leading to a drastic increase in demand for lithium for battery production. The resulting shortage of this raw material is forcing the foundry industry and its suppliers to pursue a radical new orientation.
At the same time, the issues of sustainability and social responsibility are of very high priority. Thanks to the development of a new generation of innovative, lithium-free sand additives, which are in no way inferior to conventional lithium-containing sand additives, the total amount of lithium required for the production of the additives has been reduced by 100%.
Need for sand additives in foundries
Sand additives are essentially divided into 3 groups, based on their composition and mode of action. The supplier's task is to recommend to the foundry, as an individual user, the correct additive in the correct addition percentage (sand recipe) for the specific production process. Essentially, we can state that the use of sand additives is not only decisive for maintaining or increasing competitiveness, but is essential for meeting the quality requirements of the casting. Particularly noteworthy are the good anti-cresting properties with excellent performance, even where additive addition proportions are low. In light of the above, it is not surprising that the importance of sand additives is constantly increasing.
New types of special lithium-free sand additives for foundries
Depending on the technological requirements, a combination of different organic and inorganic components is made. As an inorganic component, lithium has been shown to be effective against ridges. For this reason, for over 30 years lithium has established itself as an "all-round" ingredient not only in inorganic additives, but also in the most recent hybrid ones.
Given the circumstances, it was necessary to find a technically comparable but lithium-free alternative, which offered security in terms of supply and stability in terms of price, factors that are no longer available when using products containing lithium. After an extensive selection of alternative raw materials, a solution was found, which was first tested for properties (e.g. surface quality, resistance to bending or distortion when hot, etc.). The first tests carried out in the foundry had positive results, so the new product could be further tested with field trials.
Newly developed sand additives have proven their worth in many respects:
- significant reduction in casting defects that lead to rework or waste,
- reduction or even elimination of the addition of special sands,
- under certain conditions, it is possible to make a casting without painting,
- better metal machinability with longer tool life,
- possibility of reducing the application of release agent,
- excellent flowability of the core molding mixture with good definition of the geometries,
- additives for aluminum foundries that apply the PUCB (PhenolicUrethaneCold Box) process, with the aim of improving the dirtability of the sand,
- additives that increase the flexural strength (for cores/shapes) for the CB, Resol-CO2, Resol-methylformate (MF) processes allowing reductions in the binder.
Higher productivity thanks to cleaner equipment (phenolic urethane cold box)
Despite the application of a proven effective release agent, an accumulation of resinous pitch mixed with sand can form in a very short time, especially near the shots.
Up to a certain point, this deposit in the soul box is accepted or tolerated. After a certain number of cycles, an interruption of production for cleaning is still necessary. The addition of the additive significantly reduces both the time lost compared to standard production and the formation of pitch in the core box. After 117 cycles without cleaning the core box and without interrupting operation, the application of the release agent was drastically reduced, there was no resin build-up and it was not necessary to clean the vents.
Reduction of overall process costs
In the field of cold box manufacturing, avoiding painting probably offers the greatest opportunity to increase productivity and, with additives, ensure high quality castings. In recent years, in collaboration with the main foundries, we have worked to avoid, where possible, the painting process. This objective has been successfully achieved thanks to the new additives on numerous castings. The economic evaluation of the conventional process takes into account the overall cost of the core molding mixture, the cost of the plasters, any additives, any special sands, the management costs of the painting process and the energy costs for the drying ovens.
As a result, the paint-free process proved to be significantly more economical. In the future, taxes on the CO2 produced will also have to be considered in the calculations of potential savings. Depending on the structure of the kiln and the surfaces of the cores/moulds, this element may lead to additional five-figure costs in euros for the use of approximately 100T. of water-based plaster per year, starting from 2025.
Cost savings by replacing special sands
Specialty sands are both natural mineral sands and sintered and cast products that are produced in granular form. They are distinguished from silica sands in particular by their reduced thermal expansion, which is significantly lower in the temperature range from 20 to 800 °C.
Special sands such as chromite sand, ceramic hollow spheres, andalusite and feldspar sands are used in the casting process. The amounts added (usually 30 to 100%) vary greatly depending on your specific needs.
Special sands are an effective tool against casting defects with little or no gas and odor emissions. With a few exceptions, they are not recoverable/separable and generate high disposal costs. Beyond a certain level of accumulation, the use of specialty sands can have a negative impact on the greensand system. Furthermore, the cost of special sands can fluctuate greatly. The performance of special sands remains undisputed. However, it is necessary to ask ourselves whether the choice of forming material, as well as the quantities used, are functional to the purposes. Costs are too often accepted because no alternative can be identified to achieve the desired quality.
Increased strength in processes with RESOL-CO2 / RESOL-methylformate
Typically, the addition of conventional additives requires an increase in binder. The development of a new, patented additive makes it possible to specifically increase the strength of the core forming mixture. It is of particular interest for binder systems such as RESOL-CO2 / RESOL-MF, which require high percentages of additives in order to achieve the desired flexural strengths, but are at the same time limited by the high viscosity of the binder systems.
The newly developed additive technology allows you to increase resistance and at the same time improve fluidity. Even the reduced humidity stability typical of the system and the resistance to water-based plasters can be improved with these additives.
The strength-enhancing effect is a result of the increased fluidity of the core molding mix (physics) and the cross-linking property (chemistry) of the additive. The above translates into the following advantages for the entire process:
- prevention of casting defects, reducing the quantity of binder,
- allow or facilitate the use of water-based paints,
- improvement of fluidity and geometric definition (in the core forming phase),
- improvement of earthability after casting and shakeout,
- elimination of reinforcements in the cores (e.g. iron bars),
- increase in the shelf life of cores,
- more robust production process, i.e. a less sensitive system in case of process fluctuations.
Depending on the overall objective you wish to achieve, this aspect can be controlled through the amount of binder and/or additive. This gives the user unprecedented possibilities to realize specific requirements using lithium-free additives.
Additives for cold-box processes for improving the dirtability in Pur aluminum castings
To improve shakeout and dirtability, casters tend to reduce resin quantities and/or produce using coarser sands. At first glance, low quantities of binder are an economically and ecologically sound approach. The reduced addition of binder certainly improves the dirtability, however, the handling of the cores becomes critical. Most of the time, despite the efforts, the entire core or a large part of it remains in the casting after casting and solidification. Consequently, the residues of the core itself must be removed after shakeout, even with great efforts. The poor kneading properties of CB-bonded core forming materials therefore significantly reduce the productivity of aluminum smelting processes.
In this case, the new additive that promotes shakeout offers a significant advantage: practical tests have shown that the removal time of core residues (finishing) can be reduced by over 30-50%.
In addition to this significant improvement in productivity, the new generation of additives offers the advantages listed below:
- relatively low addition of additives (about 0.5-1.5%),
- significant improvement in de-soiling,
- possibility of reducing, in some cases, the binder,
- inorganic additive.
Powdered additives for lithium-free sands for foundries
The development of propulsion technology in the automotive sector, which has moved towards electric mobility, highlights the importance of battery production, but also the consequent dependence on lithium as a raw material. Supplies were characterized by huge price increases. Furthermore, it is important to keep in mind the disastrous effects on people, animals and the environment living in mining areas. Since lithium has been used as an essential component in many sand additives for over 30 years, a technical alternative was developed.
The new technology which involves the use of lithium-free additives offers foundries important advantages:
- increase in productivity thanks to the improvement of dirtability in aluminum castings,
- savings on raw material costs thanks to the replacement of expensive special sands,
- process cost savings and increased productivity thanks to shorter cleaning cycles,
- saving on process costs, energy saving thanks to a production cycle without painting.
Source: In Fonderia – ll magazine dell’industria fusoria italiana