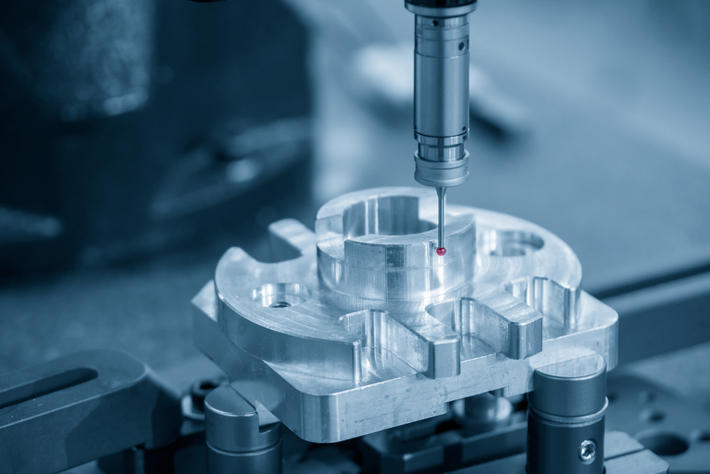
Foundry 4.0, the IoT increases productivity
The metallurgical sector invests in 4.0 technologies and plants. Thanks to the IoT, efficiency increases: the information provided by the sensors suggests changes to improve the production process and maintenance procedures, reducing energy consumption. All without losing sight of the quality of the work.
Companies in the metallurgical sector, from ferrous and non-ferrous foundries to steel producers, invest to improve competitiveness on the market: despite the difficult period, the most advanced companies face the future with new plants in Industry 4.0 logic, to introduce innovation into the factory , increasing the productivity and safety of personnel.
The foundry 4.0 and the increase in productivity
The data economy generated by 4.0 companies also makes it possible to improve the maintenance of machines, a crucial feature in a sector characterized by continuous processes, and to better manage energy consumption, an aspect which is far from negligible in an energy-intensive sector.
There are several 4.0 experiments in progress in the metal industry, such as the studies conducted in the field by the RAS (Applied Research and Sustainability) team of the Multisectoral and Technological Service Center (CSMT) of Brescia (www. Csmt.it).
With a view to revamping and updating with sensors and software of more or less dated machinery, thus made compatible with the 4.0 digitization logic, the Brescia researchers set themselves a goal: to develop applications dedicated to the interconnection between factory machinery and information systems companies, with the aim of making critical information on production processes available, to increase productivity and in view of accessing super-hyper amortization tax breaks.
In this context, the Technological Center has created an innovative algorithm for weighing the most important raw material for foundries. It is the metal scrap, in this case transported by an overhead crane, which can be quantitatively measured effectively and precisely. In this way, both the management of the scrap yard and the final processing product gain from it. The accuracy of the measurements exceeded 98%; while pauses and inefficiencies have consequently been reduced and significant savings have been obtained in the control phases of finished products.
The power of machine learning in foundry 4.0
Naturally, an evolutionary initiative of this nature then allows it to be extended to other parts of the production cycle, ensuring more careful and effective monitoring. Thus, the RAS has also developed a sensorization project for the trolleys used to supply oil to the machinery. Here, the goal is given by the collection and processing of data on the oil consumption of each station of the production process, with LoraWAN wireless technology. With this same technology, old melting furnaces for aluminum were retrofitted, for optimal temperature control. And last but not least, the integration of a nerve center network of sensors for the collection of process data on existing machinery was also planned at the CSMT.
The perspective is to monitor and analyze the quantities of interest for a company in a context of predictive maintenance and diagnostics using artificial intelligence and machine learning techniques.
New management systems Industry 4.0 and the IoT have accelerated the innovative drive of the metallurgical industry. Thanks to these two factors it has been possible to develop new management systems which, in addition to significantly improving quality monitoring, were able to create a combination between preventive and predictive maintenance, allowing for significant productivity increases for foundry 4.0.
The information relating to machine breaks and uptime, to the different types of production, as well as to the quality and costs of the product, were cross-referenced with the data from the sensors used throughout the production chain, in order to reveal unexpected correlations and suggest changes to normal routines within the production process.
The most affordable investments for industry and foundry 4.0
These strategies have already been tested in the past but, only recently, with the extreme diffusion of control and the management of big data have investments been made affordable.
An example of this was made in the past decade by researchers V.R. Radhakrishnan and A.R. Mohamed applying the Soft Sensors, in other words software in which various measurements are processed together allowing the calculation of other quantities, to the monitoring of the melting process; in fact, the control of this phase has always represented a great challenge due to the problems related to the process. In particular, the two scholars focused on measuring the compositions of the molten metal; normally these analyzes would require spectrographic techniques that can only be performed offline but, thanks to the use of software based on neural networks, the authors were able to develop a model that related 33 process variables, including the amount of molten metal , slags and their composition, with all the important constituents for alloys, reaching an error value of less than 3%.
The intelligent components of the foundry 4.0
Other simpler applications of these technologies to the metallurgical sector have been made possible thanks to the introduction of components that already have data retrieval and transmission systems in the factory, namely smart components. These allow from the first installation a constant flow of data throughout use, greatly facilitating the digitization of the company thanks to their simplicity of installation as they do not require in-depth knowledge of all its detection systems to function.
An application example that is spreading in companies that work with continuous heat treatment furnaces is the use of automatic doors that detect the presence of semi-finished products near the furnaces, analyze their shape and position and ascertain their goodness before carrying out the treatment; this allows you to discard any products that do not meet the desired standards and improve the opening and closing timing of the oven door, so as to disperse less heat and save energy.
The same detection systems with which the smart components are equipped can have a dual purpose: the aforementioned analysis of external conditions and the calculation of the remaining useful life of the component (RemainingUsefulLifetime) through the study of stresses such as stresses, vibrations and temperatures subjected. The variations of these data provide an important alarm bell with regard to the predictive maintenance of the equipment and the quality control of the foundry 4.0. For example, the detection of the temperature increase by the handling chain of a metallurgical continuous line could be related to the formation of more massive pieces than usual or to a substantial error in the forming of the alloy, with consequent modification of the thermal diffusivity, while if the movement chain itself had an increase in voltages compared to those to which it is normally subjected, this could be a sign of malfunctioning of the machinery.
Unity is strength, even in the 4.0 foundry
The knowledge of this information, which taken individually may seem irrelevant, since perhaps a little outside the classical standards, entrusted to a specialized analysis model, can lead to the identification and prevention of significant damage.
To encourage the application of data science technologies to metallurgical processes, already in 2018 the European community allocated large funds for research, which were intercepted by an Italian excellence, the Sant'Anna University of Pisa, which has developed predictive models such as:
- CyberMan4.0, aimed at improving preventive maintenance and its evolution into predictive maintenance;
- TrackOpt, aimed at implementing a ladle tracking system for all stadiums in order to optimize logistics.
The prototype versions of these systems have been tested in various large industrial companies. Since the models involve the use of sensorized components and software capable of collecting information online during production, in anticipation of future investments, other companies have begun to move towards digitization and data collection.
Even the giant Microsoft, with its Azure platform, has brought the first results in the field of big-data analysis applied to the prevention, prediction and quality of metallurgical plants.
The role of the component supplier in the 4.0 foundry is for increasing productivity
A complex activity such as the design of metallurgical plants can find valuable support in component suppliers. The machinery used in foundries requires robust, long-lasting components that are easy and comfortable to assemble and maintain. In this direction, suppliers must develop a wide range of products: from lamellar joints to elastomer joints, from convex tooth joints to modular torque limiters. All components that can be transformed into an intelligent joint conceived and designed to be mounted on 4.0 machinery.
The development of smart components equipped with integrated sensors capable of measuring, collecting and transmitting data during their operation is an action in full harmony with the principles of the fourth industrial revolution: the joints must be able to self-monitor and promptly report any kind of malfunction or malfunction that could compromise production - a major benefit for budget-conscious manufacturers.
Source: A&L Aluminum Alloys Pressure Diecasting Foundry Tecniques