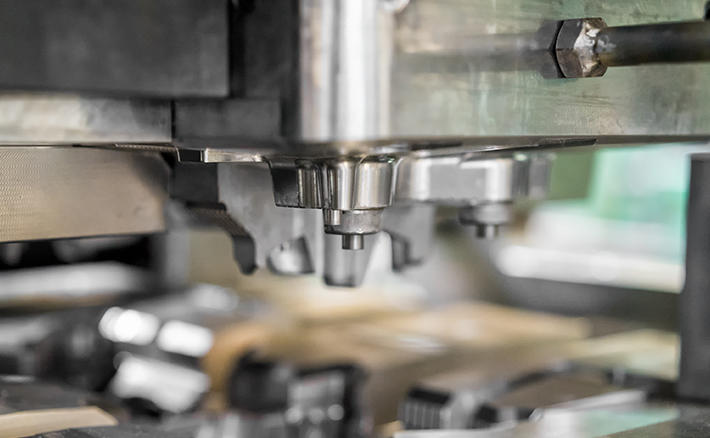
Innovation in the die-casting sector in Italy
In the field of Italian non-ferrous metallurgy, the industrial sector of aluminum die-casting has been aflagship for many years. It has always stood out for innovation: it has always been able to project itself forward, to renew technologies and improve existing ones, more than other industrial sectors in our country.
In Italy, the interest in the die casting of aluminum alloys is underlined by the number of companies that design and install machines for diecasting: there are six of them, only in Italy. Added to these are hundreds of companies that produce and supply the materials and components necessary to carry out the die-casting process. Innovation in these two sub-sectors of die-casting is constant, just think that by now industrial automation with specifically designed robots for diecasting cells has entered into a stable plant in most production companies. In addition to these, the production of die-casting molds is increasingly in-depth, the mechanical, pneumatic and electronic systems available are increasingly performing, and the processing lines are increasingly automated, also for treatments on products derived from die-casting.
The growing demand for die-casting drives the sector to innovation
In general, in Europe, innovation in the die-casting sector is growing because so too is demand: after the crisis around 2009, output returned to levels of 3.5 million tons. 75% of these jets are produced by 4 countries: first Germany, leader in the sector with about a third of the total, then coming from Italy, firmly in second place. More detached, Poland and France. In particular, the demand in the automotive sector has grown due to the quality of the aluminum, light and performing at the same time.
It is no coincidence that the main innovation in the die-casting sector is the improvement of the characteristics of the raw material and the consideration that it feeds on it: only a couple of decades ago there was talk of secondary alloys, both for the origin of the metal (from remelting) that for quality, which was considered just second level compared to other sectors. Today, thanks to the innovation of casting and casting technologies and to the new care of companies in the production in the die-casting sector. The cleaning during the fusion has improved, filtering and cleaning systems have become widespread, the installation of increasingly sophisticated control systems for the porosity of the metal and the cleaning index has been extended, software for the data recording. All this, as already mentioned, combined with the increasingly widespread introduction of automation and the use of robots, which contrary to what one might think, qualifies the role of the operator.