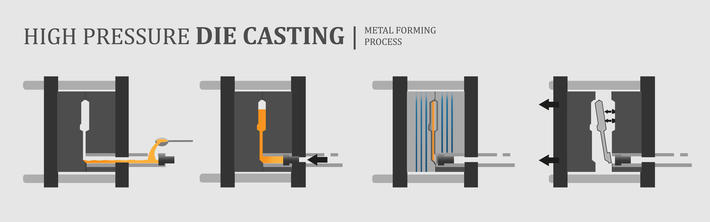
Why choose cast aluminum than other materials
Die-cast aluminium is used in every major industry, from the most sophisticated as electronics or aerospace, to the more common ones, such as automotive and car circles.
The breadth of applications of aluminium is due to the fact that it is a metal equipped with specific technological qualities: lightness (even one third of steel), electrical conductivity (second only to copper) and thermal, mechanical characteristics enhanced by the wide possibility of establishing leagues, weather resistance, plasticity, deformability, resistance to the contact of foods (and almost all liquids) and aesthetic qualities and, not least, undisputed color aluminum objects that give an unmistakable look hi-tech.
Between the characteristics of aluminum you can not forget the corrosion resistance: the metal moves higher than the low-carbon steel, and in some cases is superior even to that of stainless steel.
The ductility and malleability, particularly for aluminum die cast, allow for the production of articles with multiple features and, as said, for a variety of applications.
What is the aluminum die casting?
The process of pressure die casting is a technique relatively new metals processing. The first presses for die casting date back to the last century, just when italpres has screwed the activity at the plant in Lumezzane, import industrial district of the province of Brescia. Also known as die casting is a particular Foundry process in permanent form, in which molten metal, in this case aluminum, is injected at high pressure into a mould. This process was developed for the first time in the United States of America towards the second half of the nineteenth century.
The die-cast aluminium allows to obtain metal parts quickly and with a good degree of finish. The process consists in casting into a mould a metal alloy and then bring it to high pressures. This has some advantages that cannot be obtained with the merger. You have a flawless and perfect filling of the mold cavity and also an excellent finish.
A fundamental role in the whole process has the mold that will be subject to high pressure and temperature shock.
Source: University of Trento, Faculty of engineering materials- Francesco Zanatta